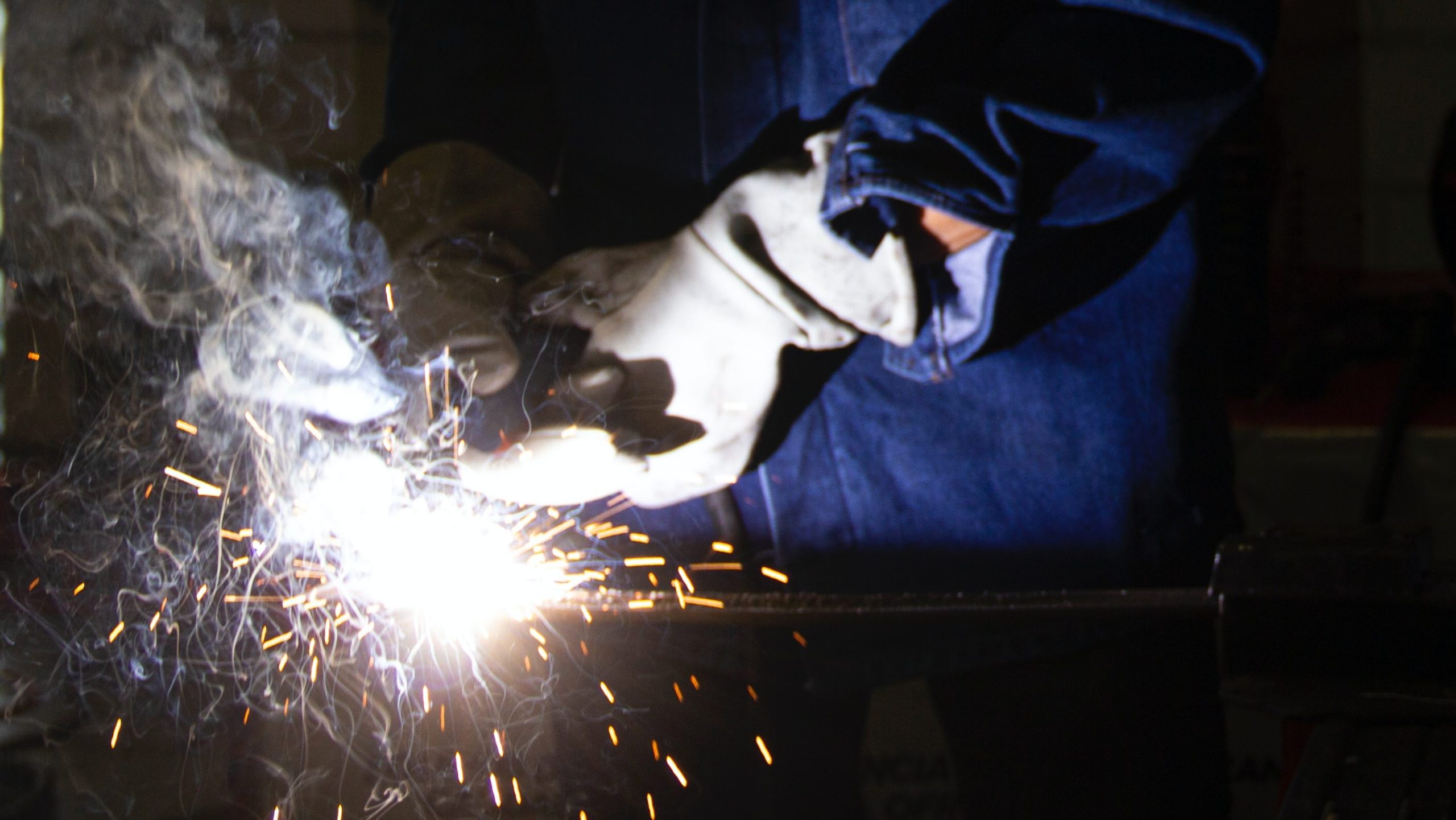
Flux-Cored Welding: The Perfect Blend of Speed and Versatility
Flux-cored welding, a versatile and efficient welding technique, offers both speed and adaptability for various applications. In this article, we’ll dive into the basics of flux-cored welding, its benefits, and how it compares to other welding methods. By the end, you’ll have a better understanding of why flux-cored welding might be the perfect choice for your next project.
Understanding the Flux-Cored Welding Process
At its core, flux-cored welding is a type of arc welding that uses a continuous, tubular wire filled with flux. This flux material acts as a shielding gas, protecting the weld from contaminants and atmospheric elements. There are two main types of flux-cored welding: self-shielded (FCAW-S) and gas-shielded (FCAW-G). Self-shielded welding does not require an external shielding gas, while gas-shielded welding uses a separate gas supply for additional protection.
The flux-cored welding process begins when an electric arc is struck between the wire electrode and the base metal, melting both the wire and the workpiece. The flux material inside the wire then vaporizes, creating a shielding gas that envelops the molten weld pool. This gas helps to prevent oxidation, ensures a cleaner weld, and allows for increased deposition rates.
Advantages of Flux-Cored Welding
Flux-cored welding offers several benefits that make it an attractive choice for many applications:
- High Deposition Rates: Flux-cored welding allows for faster welding speeds, increasing productivity and reducing overall project time.
- Versatility: This welding method works well with a variety of metals, including carbon steel, stainless steel, and some low-alloy steels. It’s also suitable for different welding positions and can be used both indoors and outdoors.
- Ease of Use: Flux-cored welding is relatively easy to learn and requires less skill compared to other welding techniques, such as TIG or stick welding.
- Reduced Clean-Up: The flux-cored process typically generates less spatter, resulting in cleaner welds and less post-weld clean-up.
- Increased Penetration: Flux-cored welding offers deeper penetration, which can lead to stronger welds, especially on thicker materials.
Comparing Flux-Cored Welding to Other Techniques
Flux-cored welding stands out from other welding methods in several ways:
- MIG Welding: While both MIG and flux-cored welding use a continuous wire feed, flux-cored welding does not always require an external shielding gas. This makes it more versatile for outdoor applications and reduces the need for additional equipment. However, MIG welding typically produces cleaner welds with less slag.
- TIG Welding: TIG welding offers precise control and clean welds, making it ideal for thin materials and intricate work. However, it requires a higher skill level and is slower compared to flux-cored welding.
- Stick Welding: Stick welding is highly versatile and doesn’t require a shielding gas, making it suitable for outdoor applications. However, flux-cored welding provides faster deposition rates and generally requires less skill.
Conclusion
Flux-cored welding is an efficient and versatile welding technique that offers several advantages, including high deposition rates, adaptability, ease of use, and reduced clean-up. While it may not be the best choice for every application, it’s a valuable method to have in your welding arsenal, especially for projects
that require speed and flexibility. Whether you’re working with carbon steel, stainless steel, or low-alloy steels, flux-cored welding could be the perfect solution for your needs.
Frequently Asked Questions
- What is the main difference between self-shielded and gas-shielded flux-cored welding?
Self-shielded flux-cored welding (FCAW-S) does not require an external shielding gas, as the flux within the wire provides the necessary protection. Gas-shielded flux-cored welding (FCAW-G) uses a separate gas supply to provide additional shielding. - Is flux-cored welding suitable for beginners?
Yes, flux-cored welding is relatively easy to learn and requires less skill compared to other welding techniques, such as TIG or stick welding. However, proper training and practice are still necessary to ensure safe and effective welding. - Can I use flux-cored welding for thin materials?
While flux-cored welding is suitable for a variety of materials and thicknesses, it may not be the best choice for very thin materials. TIG welding is often recommended for thin materials due to its precise control and clean welds. - What type of metals can be welded using flux-cored welding?
Flux-cored welding works well with a variety of metals, including carbon steel, stainless steel, and some low-alloy steels. - Do I need a special welding machine for flux-cored welding?
Flux-cored welding can be performed with most MIG welders, as long as they are equipped with the proper accessories, such as a suitable wire feeder and the correct type of wire.