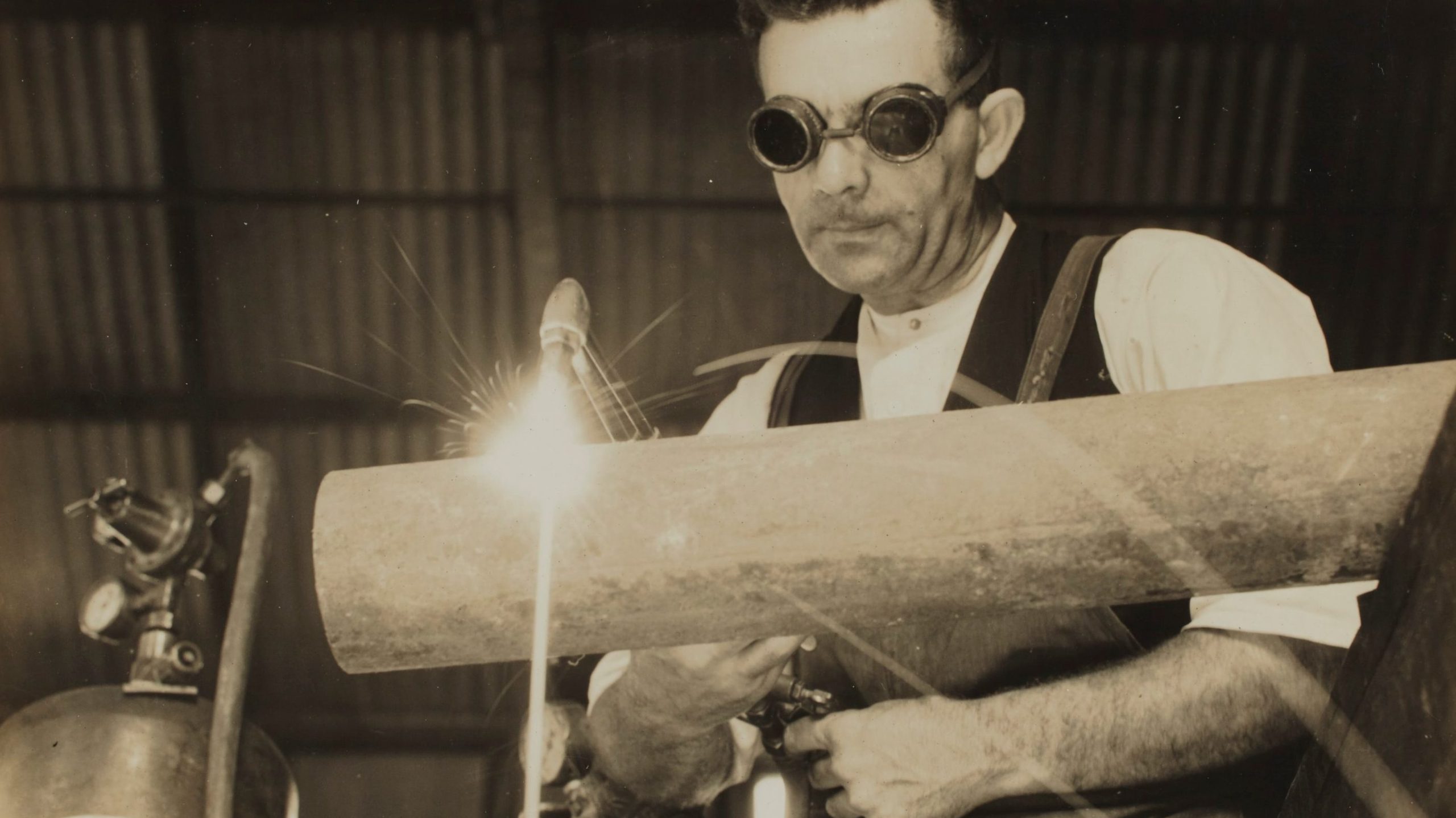
Gas welding is a popular welding technique that is used in various industries for the joining of metals. It is a welding process that uses a flame generated by burning a mixture of gases, typically oxygen and acetylene, to heat and melt the metal surfaces. Gas welding is a versatile and efficient method that can be used for a variety of applications, including construction, manufacturing, and automotive repair. In this article, we will discuss the basics of gas welding, its advantages and disadvantages, safety measures, and other related topics.
Gas Welding Basics
Gas welding involves the use of a torch that produces a flame hot enough to melt the metal. The torch is typically connected to a gas cylinder containing a mixture of gases, usually oxygen and acetylene, which are then ignited to create the flame. The heat generated by the flame is used to melt the metal surfaces that are being welded. Once the metal has melted, a filler rod is added to fill the gap between the two pieces of metal, creating a strong joint.
Advantages of Gas Welding
One of the main advantages of gas welding is that it is a relatively simple process that requires minimal equipment. Gas welding equipment is also readily available and affordable, making it a popular choice for hobbyists and DIY enthusiasts. Gas welding is also versatile and can be used to weld a wide range of metals, including steel, aluminum, and copper.
Another advantage of gas welding is that it produces a high-quality weld that is free of defects such as porosity and cracking. This is because gas welding allows for precise control of the heat input, which is critical for producing a strong and reliable weld.
Disadvantages of Gas Welding
Despite its advantages, gas welding also has some disadvantages. One of the main disadvantages is that it is a slow process that requires a high level of skill and experience to achieve the best results. Gas welding also produces a lot of heat, which can warp or distort the metal being welded if proper techniques are not used.
Safety Measures for Gas Welding
Gas welding involves working with high temperatures and potentially dangerous gases, so it is important to take safety measures to prevent accidents and injuries. Some safety measures that should be taken when gas welding include:
- Wearing protective gear such as gloves, aprons, and safety glasses to protect against sparks and hot metal
- Ensuring adequate ventilation to prevent the buildup of dangerous gases such as carbon monoxide
- Keeping a fire extinguisher nearby in case of a fire
- Ensuring that all gas cylinders are properly secured and stored in a well-ventilated area
- Checking all equipment before use to ensure that it is in good condition and functioning properly
Gas Welding Applications
Gas welding is used in a variety of industries for various applications. In construction, gas welding is used to join metal pipes and fittings. In manufacturing, it is used to weld sheet metal and other components. Gas welding is also commonly used in automotive repair for repairing body panels and exhaust systems.
Gas Welding Conclusion
In conclusion, gas welding is a versatile and efficient welding process that can be used for a variety of applications. While it has some disadvantages, such as its slow speed and high heat output, it also produces high-quality welds that are free of defects. When using gas welding, it is important to take safety measures to prevent accidents and injuries.